Riparazione delle pale del compressore


Riparazione delle pale del compressore
Aircraft engine compressor blades are high-temperature, high-pressure, high-speed rotating parts, and the working conditions are relatively harsh. The tip of the blade is prone to cavitation. If the wear exceeds a certain amount, it will fail, reduce the compression ratio, and shorten its service life. .
Replacement of new blades will greatly increase the maintenance cost and bring losses in many aspects. At present, the repair methods that can be considered and are theoretically feasible include arc welding, plasma welding, and laser powder 3D printing. Arc welding and plasma welding not only have a large amount of heat input, but also cannot solve the micro-undercut phenomenon at the air inlet and outlet edges of the blade and cause serious deformation. Laser powder coating 3D printing has low efficiency, high cost and low qualified rate for repairing blade tip.
Project sample
The adaptive laser cladding technology developed by Haitian for the thin-walled and variable cross-section of compressor blades, and the precise comparison technology of laser coaxial imaging system can greatly improve the accuracy and quality of additive repair of aviation compressor blades.
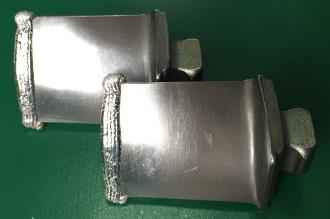
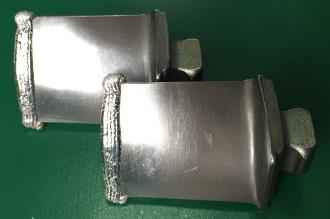
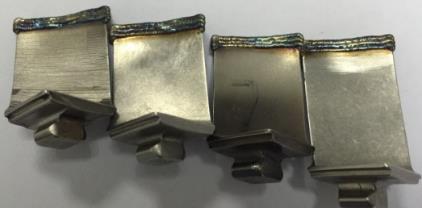
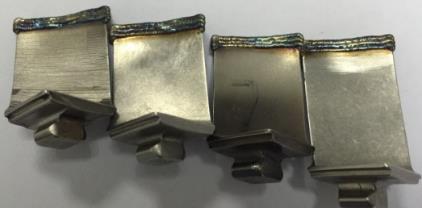
Laser fed powder 3D printing remanufacturing technology is to use high power laser beam through the focus of optical components to obtain very high energy density, instantly melt the surface of the substrate, while making the alloy powder pre-set or automatically fed to the surface of the substrate in parallel with the laser beam completely melted, to obtain a dense cladding layer metallurgically bonded with the substrate. The bond strength is generally not less than 95% of the original substrate material.
The substrate material can achieve surface microfusion during laser processing, the microfusion layer is 0.05 ~ 0.1mm, the heat-affected zone of the substrate is very small, generally 0.05 ~ 0.5mm. The cladding layer and the substrate are no coarse casting organization, the cladding layer and its interface organization is dense, small grain size, no cavities, no inclusions of cracks and other defects. Laser processing process substrate temperature rise does not exceed 80 ℃, laser processing after the deformation to 0.01mm calculation, after heat treatment stress relief, deformation will be calculated by 0.001mm, has been completely can be slightly.
Due to the blade tip thickness changes, the middle thickness is the largest, melting when the larger power is required. If the laser to the same power for melting, the two ends of the thinnest place will be this larger power melting, can not play a role in repair. Therefore, in order to get both the corresponding melting width and not melt the blade ends of the material, using variable power melting. As the blade ends are particularly thin, 8 level blade ends thickness is only 0.2mm. in the laser melting easy to produce edge biting phenomenon, so need to make special treatment in both ends, can solve the problem of edge biting. In the low-power melting must rely on the laser coaxial imaging system for accurate more points. At present, the repaired rotor blades of the compressor have good results.